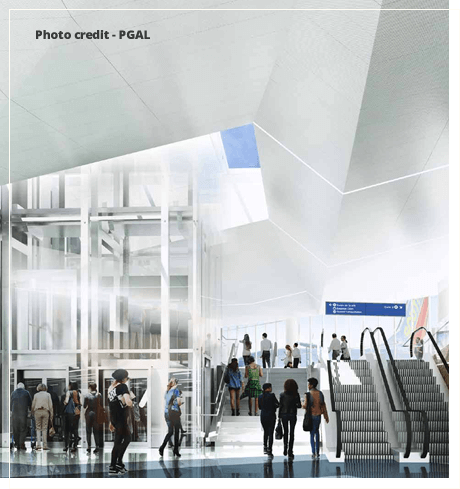
Southwest Terminal 1 Renovation
This $509.8 million renovation project will enhance the 31-year-old existing terminal by improving the interior, the outdoor aircraft parking ramp area, and the traffic flow around the Central Terminal Area of Los Angeles International Airport (LAX).
CONSTRUCTION BEGIN: August 2014, COMPLETION DATE: Summer 2018
THE PROJECT INCLUDES:
- 346,000 Square Feet of Renovated and Upgraded Space
- 61,000 Square Feet of New Space
- 13-Gate facility
- New Enlarged Hold Rooms with Expanded and Integrated Concessions
- Tier 1 Los Angeles Green Building Code (LAGBC)- Many finishes specified on the project have recycled content including the holdroom carpeting that is made from re-purposed waste nylon from discarded fishing nets.
- All exterior glazing in the building is being replaced and meets the new Tier 1 LAGBC July 2015 requirements. All the building systems are being modernized including the HVAC systems, Electrical, Gas, Water and waste systems, to meet Tier 1 LAGBC July 2015 requirements